In the vast world of manufacturing, the processing service of non-standard automated spare parts plays a crucial role. It is not only the cornerstone of the flexibility and efficiency improvement of the production line but also an important driving force for promoting industrial upgrading and innovation. This article will deeply explore the processing service process of non-standard automated spare parts, fully revealing this complex and delicate process from demand analysis, design planning, material procurement, precision processing, quality inspection to installation and commissioning.
- Demand Analysis: The Starting Point of Customized Demands
The processing of non-standard automated spare parts begins with the precise grasp of customer demands. This process involves in-depth communication with customers to understand the specific functional requirements, usage environment, performance parameters and special needs of the product. The project manager and technical team will conduct a preliminary demand analysis and feasibility assessment based on this information to ensure that the solution not only meets customer needs but also conforms to technical feasibility and cost control principles. Through detailed demand documents, a solid foundation is laid for the subsequent design work.
- Design Planning: The Collision of Creativity and Technology
Design is the soul of the processing of non-standard automated spare parts. After clarifying the demands, the design team will use advanced tools such as CAD (Computer-Aided Design) and CAE (Computer-Aided Engineering) to conduct three-dimensional modeling and simulation analysis. This process aims to optimize the structural design and ensure that the stiffness, strength, precision and durability of the spare parts meet the requirements. At the same time, the processability of processing also needs to be considered to ensure that the design solution can be efficiently transformed into a physical object. After the design is completed, internal reviews and customer confirmations will be conducted to ensure the accuracy of the design solution.
- Material Procurement: The Balance of Quality and Cost
The selection of materials is directly related to the performance and cost of non-standard automated spare parts. The procurement department will search for raw materials and components that meet the requirements worldwide based on the design specification. While focusing on quality, efforts will also be made to reduce costs and improve the overall cost performance through negotiations, price comparisons and other methods. In addition, for key materials, strict supplier reviews and incoming inspections will be conducted to ensure that each piece of material meets the quality requirements.
- Precision Processing: The Fusion of Skills and Equipment
Entering the processing stage, the production of non-standard automated spare parts enters the most critical link. In the processing workshop, high-precision equipment such as CNC machine tools, laser cutting machines and electrical discharge machining machines stand in rows. Under the meticulous control of the operators, they carve each piece of raw material into complex spare parts. This process has extremely high requirements for processing precision, surface quality and dimensional stability. Therefore, during the processing, it is necessary to strictly follow the process regulations and implement process monitoring to ensure that each operation meets the design requirements.
- Quality Inspection: The Guardian of Quality
Quality inspection is an indispensable link in the processing process of non-standard automated spare parts. After the processing is completed, the quality inspection department will conduct a comprehensive inspection of the spare parts according to relevant standards and technical requirements. This includes but is not limited to dimension measurement, geometric tolerance detection, material performance testing and functional verification. Through a strict quality control system, it is ensured that each piece of spare part leaving the factory can meet the quality standards expected by customers. For unqualified products, rework or scrap treatment will be carried out, and no flaws will be allowed to flow into the next link.
- Installation and Commissioning: The Leap from Blueprint to Reality
The last step is to install the non-standard automated spare parts into the customer’s equipment or system and conduct commissioning and operation. The installation team will formulate a detailed installation plan according to the on-site situation and strictly implement it. During the installation process, attention also needs to be paid to the coordination and interface issues with other components to ensure the coordinated operation of the overall system. During the commissioning stage, technicians will conduct a comprehensive test of the system, adjust parameters and optimize performance until it reaches the optimal operating state. Finally, the acceptance by the customer marks the successful conclusion of the entire processing service process.
The processing service process of non-standard automated spare parts is a complex and delicate systematic project, which covers multiple links such as demand analysis, design planning, material procurement, precision processing, quality inspection and installation and commissioning. In this process, each link is crucial, and any oversight in any link may lead to the failure of the final product. Therefore, only by continuously optimizing process management and improving technical level and service quality can one remain invincible in the fierce market competition. With the continuous development and upgrading of the manufacturing industry, the processing service of non-standard automated spare parts will also usher in a broader development prospect.
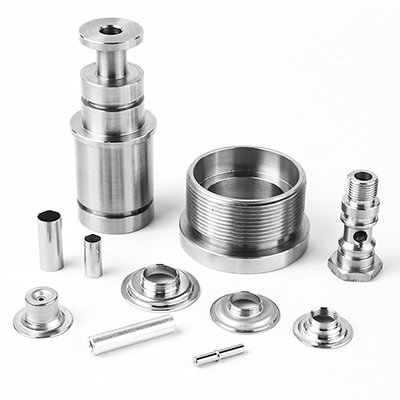
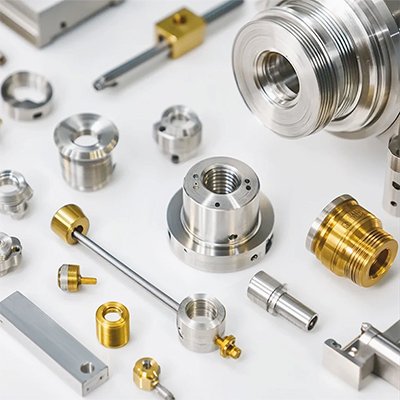